Alstom ha acquistato tre fresatrici Correa per il proprio stabilimento nella Repubblica Ceca. Il progetto, dal valore di svariati milioni di euro, contribuirà a rendere più performante la lavorazione dei carrelli per il settore ferroviario. Con le nuove macchine Correa è stato possibile ottimizzare i processi produttivi, riducendo i tempi circa del 20%
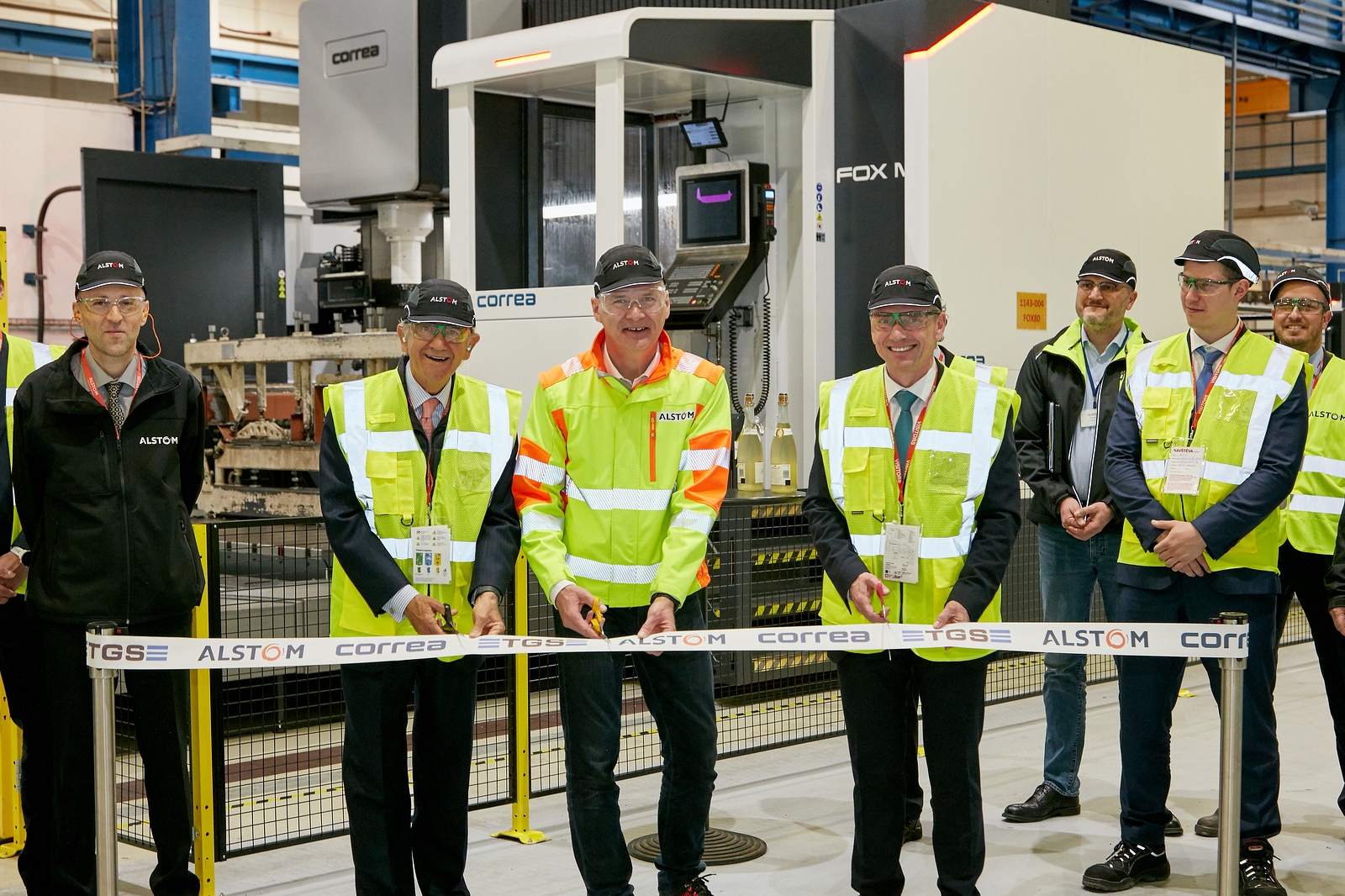
La multinazionale francese Alstom ha acquistato tre fresatrici a portale Correa per il proprio stabilimento di Česká Lípa, nella Repubblica Ceca. In questo stabilimento si producono pezzi per treni locali, tram, metrò e altri veicoli ferroviari; con quasi 1.300 dipendenti, è una delle aziende più importanti della regione. Il progetto, dal valore di svariati milioni di euro, include una fresatrice a ponte fisso FOX-40 e due fresatrici tipo gantry FOX M-80 ed è stato approntato congiuntamente con TGS, distributore di Correa nella Repubblica Ceca. La macchina FOX-40 presenta corse di 4.000 mm lungo l’asse X, 3.000 mm su Y, 1.000 mm su Z e una testa universale automatica UAD. Le due macchine tipo gantry FOX M-80 sono attrezzate con tre teste ciascuna e presentano corse di 8.000 mm lungo l’asse X, 4.250 mm su Y e 1.500 mm su Z. Il processo di produzione dei pezzi era un aspetto critico che è stato possibile ottimizzare con le nuove macchine Correa, riducendo di circa il 20% i tempi di lavorazione dei vari pezzi eseguita da Alstom. Alla cerimonia allestita in occasione dell´avviamento delle tre macchine, lo scorso 26 aprile, hanno partecipato José Nicolás-Correa, presidente del Gruppo Correa e José Manuel Revuelta, capo dell´Ufficio economico e commerciale dell´Ambasciata di Spagna a Praga.
Stretta collaborazione con TGS
L´azienda ceca TGS è il fornitore locale di Alstom ed è permanentemente in contatto con il reparto di lavorazione per soddisfare le sue esigenze, sia a livello di utensili da taglio che di supporto tecnico. Per questo progetto occorreva conoscere a fondo il processo di lavorazione dei pezzi per essere in grado di ottimizzarlo e di mettere a punto una soluzione completamente adattata all´applicazione del cliente. TGS ha partecipato a numerose riunioni con il reparto di lavorazione di Alstom per studiare i tempi e progettare il processo per migliorare i tempi con i mezzi produttivi a disposizione. "Abbiamo affrontato la progettazione e la soluzione tecnologica del processo per garantire la sicurezza del comportamento delle macchine, dei programmi e di tutti i processi di servizio, senza richiedere interventi manuali dei tecnici. La continuità della produzione è molto importante per i processi successivi e per la logistica di un prodotto di grandi dimensioni come il telaio del treno", ha dichiarato Pavel Diviš, direttore di TGS. Secondo lui, le macchine spagnole sono tra le migliori al mondo e TGS è rappresentante esclusivo di Correa nella Repubblica Ceca.
Teste robuste
Lo stabilimento di Alstom a Česká Lípa si dedica alla costruzione di carrelli, pezzi realizzati con saldatura meccanica, di grandi dimensioni e dalle forme complesse con sporgenze e rientraze, il che complica il processo di lavorazione. Questa tipologia di pezzi vibra molto durante la lavorazione. Queste vibrazioni provocano, tra gli altri inconvenienti, un´usura più rapida delle teste e perciò Alstom si trovava a dover effettuare spesso interventi sulle teste delle macchine di altri costruttori. Il fermo macchina è un fattore critico per Alstom dato che la sua produzione è programmata 7 giorni alla settimana, 24 ore al giorno. La tecnologia delle teste Correa è estremamente idonea a questo tipo di operazioni, in quanto le teste sono molto rigide, stabili e meccaniche al 100% e al loro interno non contengono elementi delicati che potrebbero danneggiarsi facilmente durante le operazioni di lavorazione più gravose. Tra l´altro, l´asse principale della testa è supportato da 6 cuscinetti ed è particolarmente performante in questo tipo di applicazioni. Per questo progetto è stata appositamente allestita una testa per l´applicazione del cliente. La testa angolare Correa standard era ISO 50 e non consentiva di accedere ad alcune parti del pezzo. Nemmeno le teste angolari reperibili sul mercato rappresentavano una soluzione accettabile, per mancanza di rigidità o perché le loro dimensioni non consentivano di lavorare nelle zone dall´accesso più difficoltoso. La soluzione di Correa è una testa angolare ISO 40 fissata direttamente allo slittone, ottenendo così una maggiore rigidità e la compatibilità con il sistema di cambio automatico teste. Inoltre, nella macchina sono state inserite teste angolari reperibili in commercio, per l´esecuzione di operazioni puntuali meno gravose. L´Ufficio di ingegneria di Nicolás Correa ha allestito questa soluzione in modo tale che l´accoppiamento di quest´ultimo tipo di teste sia completamente automatico (adattamento al sistema di cambio utensili e progettazione di un “stop-block” o blocco per il fissaggio di questa testa più adatto rispetto agli elementi standard reperibili).
Soluzioni su misura
Come tutte le macchine Correa, anche in questo caso sono state adattate all´officina del cliente e alle sue esigenze di lavoro; per garantire un´elevata disponibilità della macchina, è stata predisposta una testa di ricambio per evitare fermi macchina e condizioni speciali di assistenza con risposta in tempi brevi. “Alstom aveva bisogno delle macchine in breve tempo e la tempistica concordata era molto ristretta. Nonostante le difficoltà degli ultimi mesi, Correa è riuscita a costruire e a installare le macchine rispettando i tempi di consegna nonostante la crisi delle materie prime, la ritardata consegna degli elementi reperibili in commercio, l´aumento dei prezzi, ecc.” spiega Raúl de la Peña, Area Manager di Nicolás Correa nella Repubblica Ceca. Nel capitolato d´appalto di Alstom erano inclusi i disegni di vari pezzi per eseguire lo studio dei tempi allo scopo di garantire un miglioramento di circa il 20% sui tempi di lavorazione di ogni pezzo. Fino a quel momento, nello stabilimento di Česká Lípa la lavorazione dei telai era eseguita su varie macchine. Per il nuovo progetto era rischiesto l´impiego di una singola macchina, eliminando i tempi morti tra le macchine, automatizzando al massimo il processo e minimizzando la manodopera necessaria. TGS dispone di una fresatrice FOX presso le proprie strutture e gli ingegneri di Alstom insieme a quelli di TGS hanno eseguito vari test su questa macchina perfezionando i progetti di CAM, valutando ogni singola operazione per individuare i miglioramenti possibili. Infine, occorre sottolineare che per ottimizzare il processo di lavorazione dei pezzi, sono stati progettati attrezzi speciali che TGS ha costruito presso le proprie strutture.