Alstom acquiert trois fraiseuses Correa pour son usine de République tchèque. Le projet, d’une valeur de plusieurs millions d’euros aidera à accroître l’efficacité de l’usinage de bogies pour le secteur ferroviaire. Les nouvelles machines Correa ont permis d’optimiser les processus de fabrication, en réduisant les temps sur tour de 20%
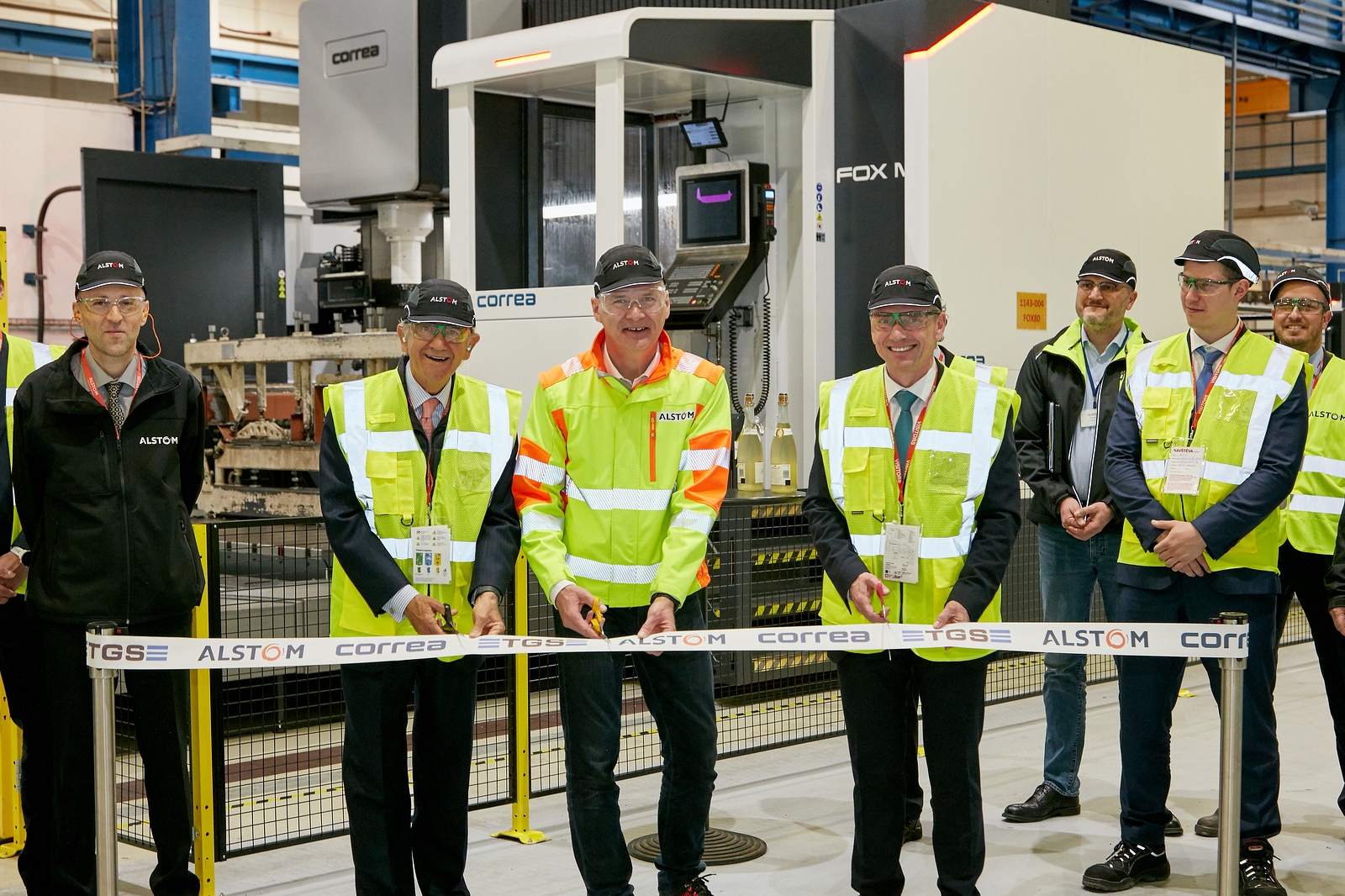
La multinationale Française Alstom a acquis trois fraiseuses à portique Correa pour son usine de Česká Lípa, dans la République tchèque. Cette usine produit des pièces pour des trains de banlieue, des tramways, le métro et d’autres véhicules ferroviaires ; avec près de 1 300 employés, c’est l’un des plus importants employeurs de la région. Le projet, d’une valeur de plusieurs millions d’euros se compose d’une fraiseuse à pont fixe FOX-40 et de deux fraiseuses de type gantry FOX-M-80 et il a été réalisé conjointement avec TGS, distributeur de Correa dans la République tchèque. La machine FOX-40 possède des parcours de de X 4 000 mm, Y 3 000 mm, Z 1 000 mm et une tête universelle automatique UAD. Les deux gantrys FOX M-80 sont équipées de trois têtes chacune et elles disposent de 8 000 mm sur l’axe X, 4 250 mm sur Y et 1 500 mm sur l’axe Z. Le processus de fabrication des pièces était un aspect critique qui a pu être optimisé avec les nouvelles machines Correa, en réduisant les temps sur tour de 20% sur les différentes pièces usinées par Alstom. L’acte réalisé en raison de la mise en marche des trois machines, le 26 avril, a bénéficié de la présence de M. José Nicolás-Correa, Président du groupe Correa et M. José Manuel Revuelta, Conseiller principal du Bureau économique et commercial de l’Ambassade d’Espagne à Prague.
Étroite collaboration avec TGS
L’entreprise tchèque TGS est le fournisseur local d’Alstom et elle était en contact permanent avec son atelier d’usinage pour couvrir ses besoins aussi bien concernant les outils de découpe que l’assistance technique. Dans ce projet il était nécessaire de connaître à fond le processus d’usinage des pièces pour être capables de l’optimiser et de créer une solution entièrement adaptée à l’application du client. TGS a tenu de nombreuses réunions avec le département d’usinage d’Alstom pour réaliser une étude des temps et un design du processus qui améliorait les temps d’usinage qu’ils avaient avec leurs moyens de production. « Nous avons traité le design et la solution technologique du processus pour que le comportement des machines, des programmes et tous les processus de service soient sûrs et ne nécessitent pas d’interventions manuelles des techniciens. La continuité de la production est très importante pour les processus ultérieurs et la logistique d’un produit aussi grand que le châssis du train », a déclaré Pavel Diviš, directeur de TGS. Selon lui, les machines espagnoles sont parmi les meilleures du marché et TGS représente exclusivement ce fabricant en République tchèque.
Des têtes robustes
L’usine d’Alstom Česká Lípa se consacre à la fabrication de bogies, pièces mécanosoudées, de grande taille et formes complexes avec des parties saillantes et des languettes, ce qui complique le processus d’usinage. Cette typologie de pièce a tendance à vibrer pendant les opérations d’usinage. Ces vibrations provoquent une usure plus rapide sur les têtes, entre autres inconvénients et pour Alstom il était assez habituel d’avoir à réaliser des interventions sur les têtes des machines qui venaient d’autres fabricants. Ces arrêts de machine étaient un facteur critique pour Alstom, car sa production est programmée 7 jours sur 7, 24 heures sur 24. Pour ce type d’opérations, la technologie des têtes Correa s’adaptait très bien, car ce sont des têtes très rigides, stables et 100% mécaniques, sans éléments délicats à l’intérieur qui peuvent facilement s’endommager durant les opérations d’usinage exigeantes. Entre autres aspects, l’axe principal de la tête est supporté par 6 roulements pour pouvoir donner des prestations correctes dans ce type d’applications. Pour ce projet, une tête spécifique a été fabriquée pour l’application du client. La tête Correa coudée standard était ISO 50 et ne permettait pas d’accéder à certaines parties de la pièce. Toutefois, les têtes coudées commerciales n’étaient pas non plus une solution acceptable, que ce soit par manque de rigidité ou parce que leurs dimensions ne permettaient pas d’usiner dans les zones d’accès difficile. La solution de Correa a été une tête coudée ISO 40 directement fixée sur le bélier donnant une plus grande rigidité et compatible avec le système de changement automatique de têtes. De la même manière, des têtes coudées commerciales ont été intégrées dans la machine pour des opérations ponctuelles moins exigeantes. Le département d’Ingénierie de Nicolás Correa a préparé cette solution de telle manière que l’accouplement de ces têtes commerciales soit entièrement automatique (adaptation dans le système de changement d’outils et conception d’un « stop-block » ou blocage pour la fixation de cette tête, plus approprié que les éléments commerciaux standard).
Des solutions sur mesure
Comme toutes les machines de Correa, elles ont été adaptées à l’atelier du client et aux exigences de son travail ; pour garantir une disponibilité de machine élevée, une tête de rechange a été incluse pour éviter des arrêts de machine et des conditions spéciales de serve avec un temps de remplacement bref. « Alstom avait besoin des machines dans un bref délai de livraison et les délais qui ont été convenus étaient très courts. Malgré les difficultés des derniers mois Correa est parvenu à fabriquer et installer les machines en respectant ces délais de livraison et en affrontant la crise des matières premières, aux délais de livraison des éléments commerciaux beaucoup plus longs, à l’augmentation des prix, etc. » explique Raúl de la Peña, Directeur de secteur de Nicolás Correa en République tchèque. Le cahier des charges d’Alstom incluait les plans de plusieurs pièces pour l’élaboration d’études de temps, pour lesquelles il fallait garantir une amélioration sur tour de 20% des temps de production de chaque pièce. Jusqu’alors, les châssis de Česká Lípa étaient usinés sur plusieurs machines. La condition du nouveau projet était d’utiliser une seule machine, en améliorant de manière notable les temps morts entre les machines et en automatisant le processus au maximum en réduisant la main-d´œuvre nécessaire. TGS dispose d’une fraiseuse FOX dans ses installations et les ingénieurs Alstom eux-mêmes avec ceux de TGS ont réalisé des tests sur cette machine en perfectionnant les projets de CAM, en vérifiant opération par opération et en détectant d’éventuelles améliorations. Enfin, il convient de souligner que pour optimiser le processus d’usinage des pièces, des outillages spéciaux ont été conçus et ils ont fabriqués par TGS dans ses installations.